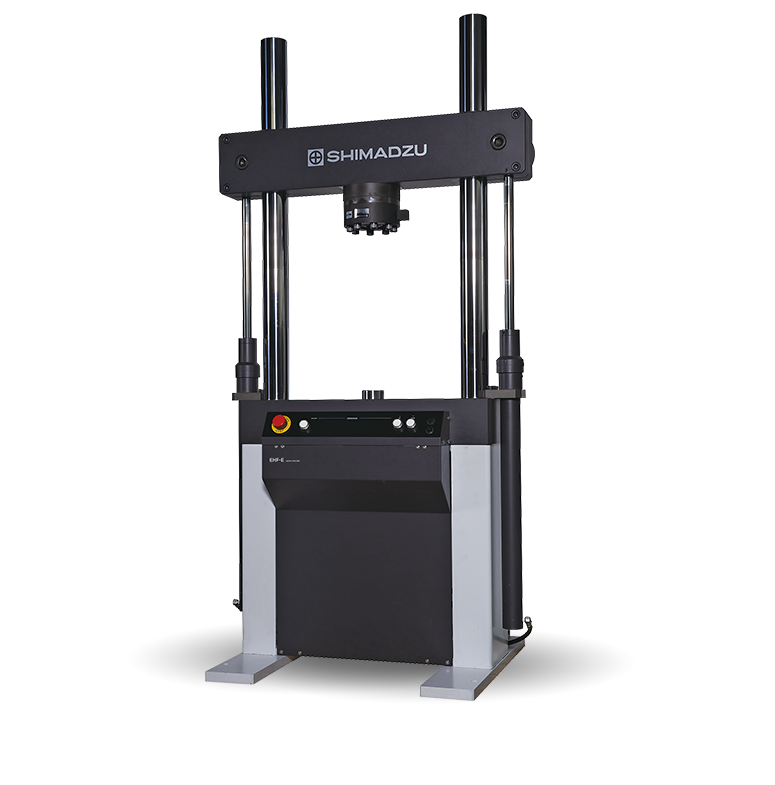
EHF-E
Electric Hydraulic Dynamic and Fatigue Testing Machine
Test force | 50, 100, 200 kN |
Test type | Tensile, bending & compression tests |
Drive | Electric Hydraulic mechanical |
Type | Floor-standing appliances |
Industries | Dynamic |
Your Partner for Dynamic and Fatigue Tests
The level and complexity of product reliability and safety requirements have been increasing in many industrial elds. Complying with such requirements requires performing a wide variety of tests and evaluations at each stage of production, from research and development of materials to evaluation of nished products. Materials and parts can sometimes form cracks from repeated exposure to even small forces and, in the worst case, even completely fail. Therefore, for products that are exposed to repetitive loads, such as automobiles, mobile phones and other frequently handled items, and arti cial bones and other biological materials or implants, it is essential that materials, parts, and nished products be evaluated by dynamic/fatigue testing and endurance/reliability testing. In addition, to more closely approximate actual usage conditions, an increasing number of tests used in research and development of various materials with special functional properties require more complicated and accurate control or measurement methods. Therefore, Shimadzu offers a wide variety of testing machines that can be con gured to satisfy increasingly sophisticated and diverse evaluation and testing requirements in a wide range of elds.
Servopulser Series Dynamic and Fatigue Testing Machines
Dynamic and Fatigue Test Machines Servo Pulser Series
Servo-hydraulic actuators are able to apply a wide range of loads, from small to large test forces. Therefore, they are ideal for fatigue testing of materials and a wide range of other dynamic testing applications. Backed by Shimadzu’s extensive experience-making actuators, frames, and controllers, these systems are capable of a wide variety of tests and evaluations.
High Accuracy and Reliability
Dynamic and fatigue testing machines are used to measure the behavior and response characteristics of materials, products, and structural members in response to varied loads. Extremely sophisticated testing control capabilities are required for controlling the waveform of the load input, from a basic sine wave to waveforms that simulate earthquakes or the loading behavior experienced in actual usage. Shimadzu Servopulser dynamic and fatigue testing systems are based on Shimadzu’s extensive dynamic testing and design technology expertise. They provide high-quality solutions for a wide variety of material testing and dynamic component evaluation applications.
- High-rigidity loading frame
- Low-friction actuator
- Controller with high waveform reproducibility and easy operability
- Software capable of diverse testing requirements andcompliant with the testing standards
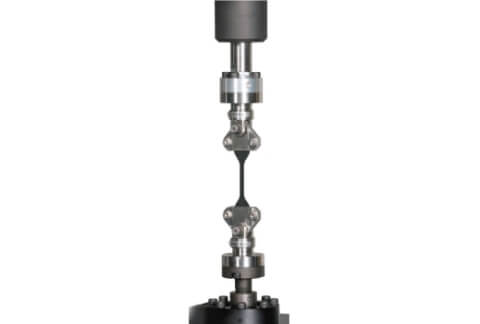
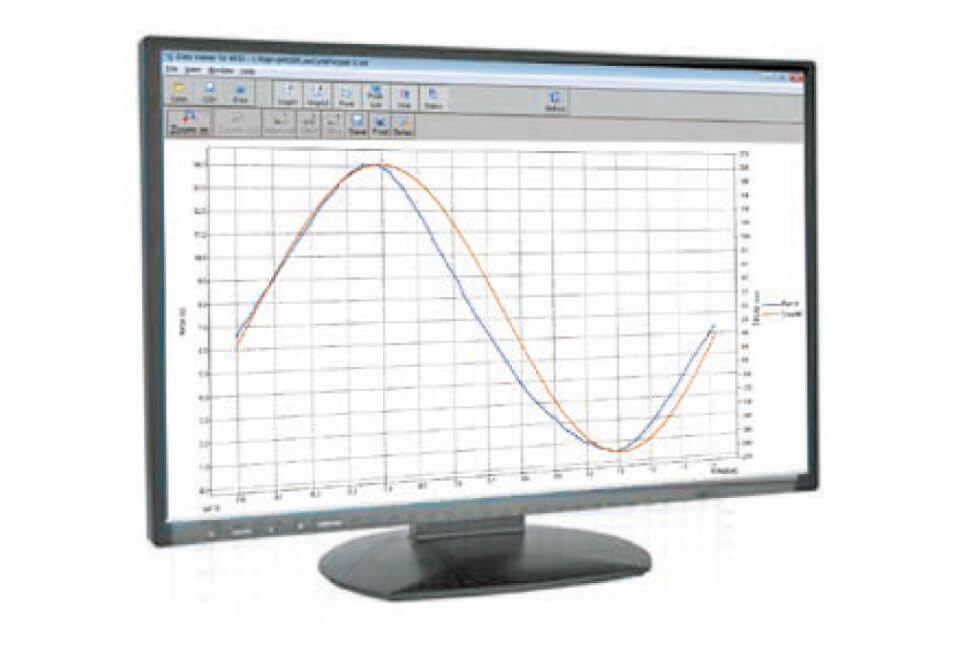
Designed for User-Friendly Operability
The Servo Controller 4830 for Servopulser series dynamic/fatigue testing machines features both an LCD touch panel and physical keys. This allows users to specify test settings and operate actuators easily and intuitively. An automatic gain control function ensures that input waveforms are reproduced accurately, which is especially important for fatigue testing. In addition to improving the ef ciency of testing, it also provides assistance for users performing tests for the rst time.
Easy Operability and Broad Applicability
The LCD touch panel and jog dial allow users to specify test parameter settingsor change parameters such as frequency, test force, or displacement at any time during tests. It also consolidates the various functions required for testing, suchas real-time display of time graphs, X-Y graphs, and peak graphs, in a single
location.
Automatic Gain Control Function Ensures Waveforms are Reproduced Accurately
When con guring parameter settings for fatigue testing, or other tests that involve repetitive waveforms, tuning and optimizing control parameter settings can be very time-consuming. However, by entering approximate settings, the automatic gain control function can be used to correct the speci ed signal so that the peak measurement values are consistent with speci ed parameters. In cases where the settings must be changed frequently for testing a variety of
materials or because the intended amplitude cannot be maintained due to fatigue degradation during the fatigue testing process, the automatic gain control function ensures that input wavefor
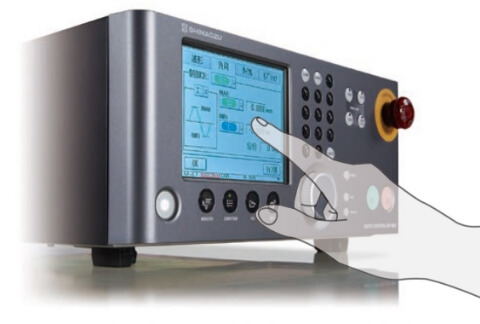
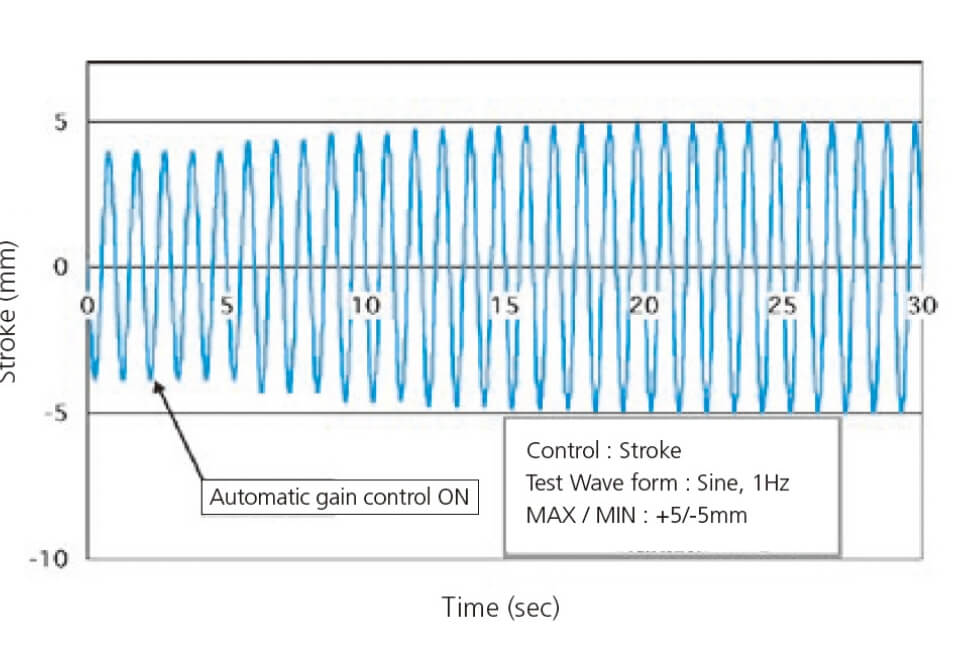
Easier, More Convenient, and More Sophisticated Testing
Windows Software for 4830
Allows users to perform a variety of tests, such as material fatigue testing, programmed testing that combines various control waveforms, and static testing. Optional software is also available for performing more sophisticated tests, easily, such as multi-axis working waveform simulation tests, multi-axis combination sine wave tests, frequency-sweep tests, and resonance frequency tracking tests, in an easier manner.
GLUON 4830 Software for Fracture Toughness Testing Compliant with the Standards
Using Shimadzu’s Servopulser with fracture toughness test software allows use of simple procedures to perform
complicated tests that comply with the standards, such as crack propagation tests, KIC/CTOD tests, or JIC tests.
ASTM E647-13,
ISO 12108:2012
ASTM E399-12, ISO 12737-96
BS 7448-1:1991,
ASTM E1820-11
ASTM E1820-11,
ASTM E813-89
JIS Z 2284-98
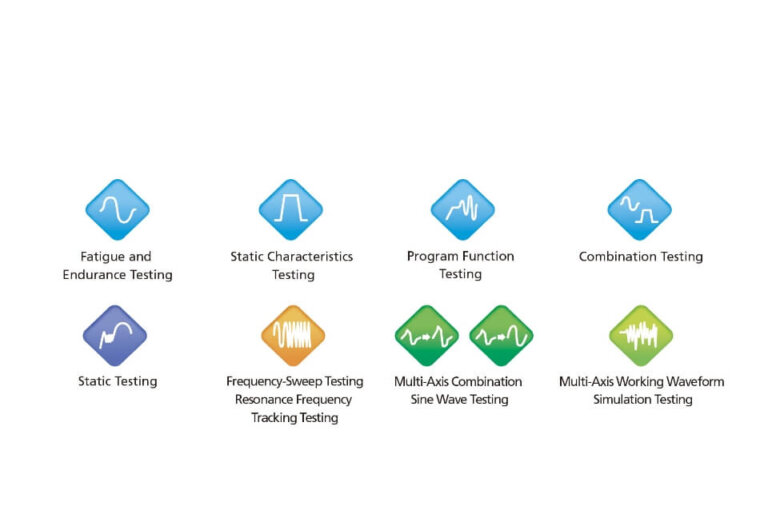
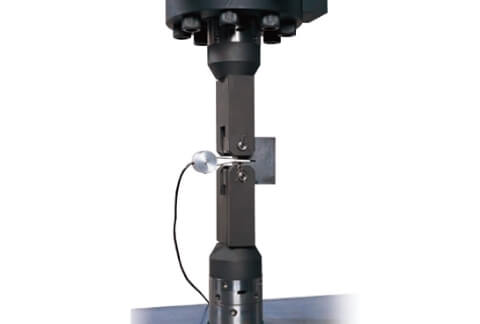
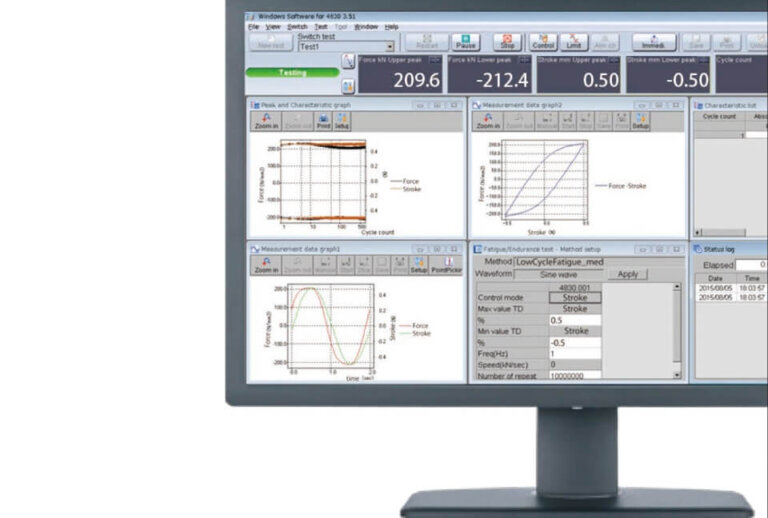
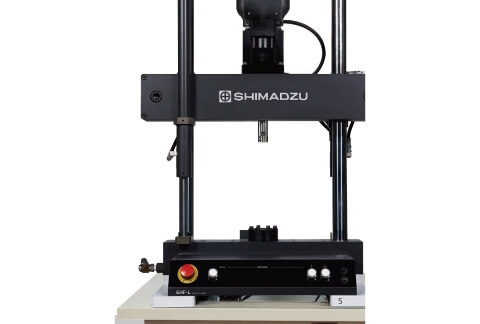
Safety
Both hardware and software help ensure operator safety by positioning emergency stop buttons, crosshead adjustment buttons, and other important switches where they are easy to operate.
Dual-Stage Crosshead Drive Mechanism
The crosshead vertical actuation system is equipped with various safety features, such as a two-stage operation for raising or lowering the crosshead and stoppers to prevent grips from falling off. A safety cover can also be installed to protect operators from ying debris.
Anti-Spiking Mechanism for Hydraulic Power Supply Unit Startup
This mechanism prevents spiking during hydraulic power supply unit startup by setting control deviations to zero.
Contact Load Function
This prevents applying excessive loads during manual actuator operations, such as when mounting or removing test samples.
Various Software Alarms
Numerous software and controller limit functions and post-limit actions ensure that even unattended operations are safe.
Stable Input Waveform
Due to the highly controlled response and accurate waveform reproducibility of Shimadzu dynamic and fatigue testing machines, they can apply loads to products based on highly precise input waveforms. Providing such a stable input waveform ensures that material fatigue testing can be performed with high accuracy and high reproducibility. Therefore, even slight differences in product performance or endurance can be evaluated.
- 24-Bit High Resolution World’s Highest Resolution
- Two-Degree-of-Freedom PID Control
- 10 kHz High-Speed Feedback World’s Fastest Feedback
- Autotuning and Automatic Gain Control Functions
Two-Degree-of-Freedom PID Control Minimizes Effects from External Disturbances
The control method (two-degree-of-freedom PID control) is able to optimize the target response for specified signals and the response to external noise. Optimizing the control parameters using the autotuning feature helps maximize the system performance. The 24-bit high-resolution measurement function and 10 kHz high-speed feedback ensure even sharp changes in test force or stroke can be controlled reliably.
Autotuning Function
The autotuning function accurately reproduces target waveforms by automatically determining optimal control parameters. Simply set up the sample in a similar state as for the intended testing and then specify the preload. Then the function automatically tunes the manually adjusted control parameters.
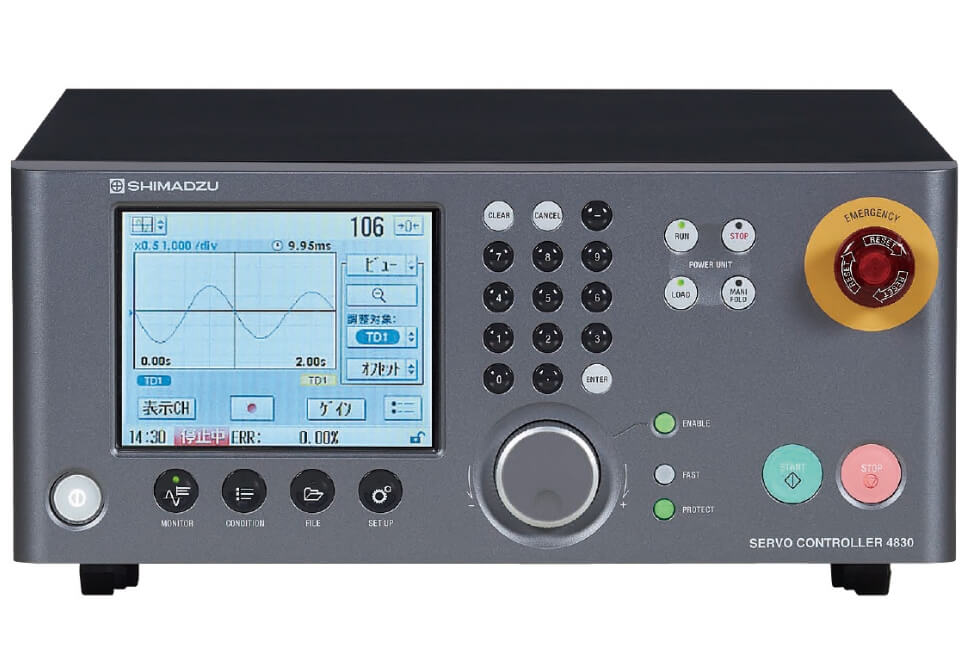
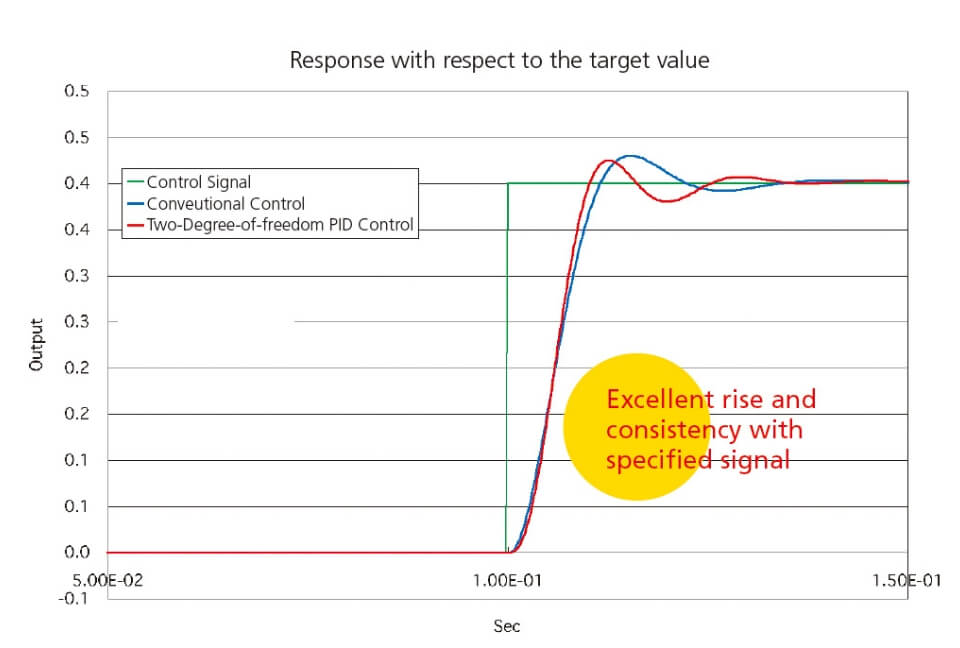
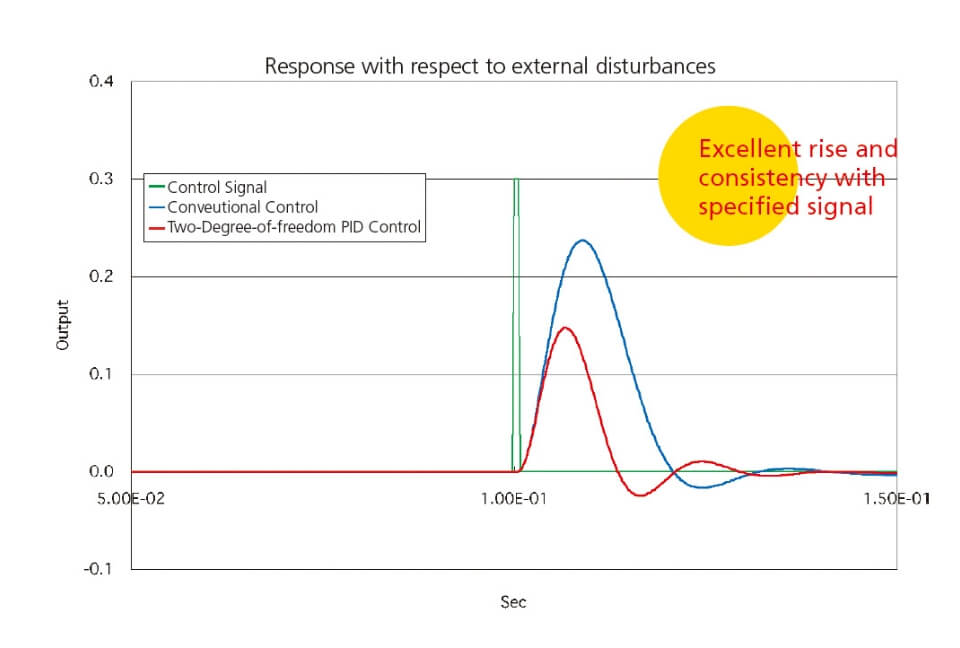
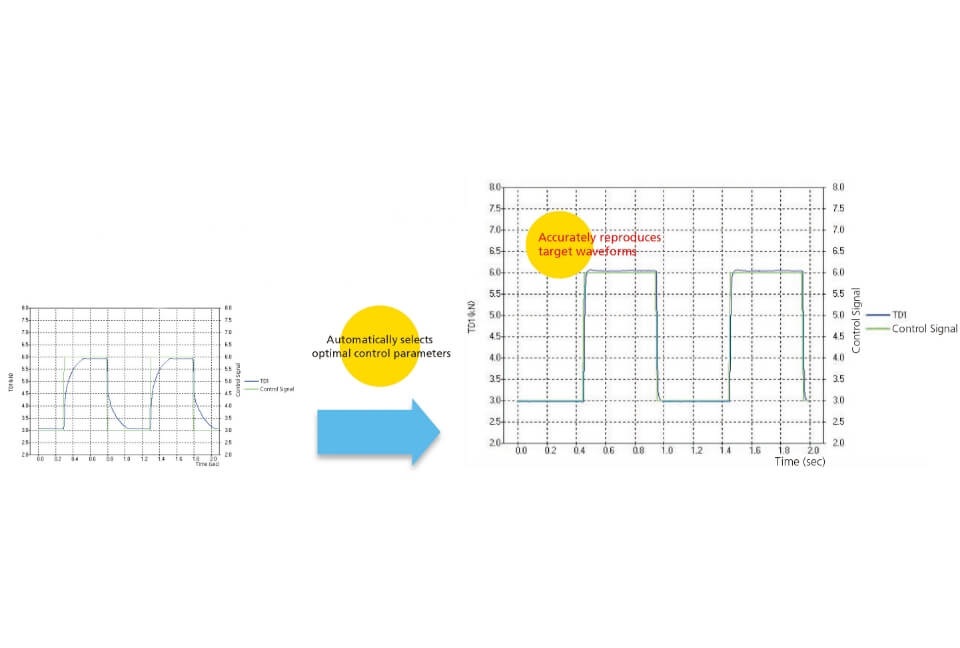
Measures Even Slight Differences in Performance
Dynamic testing machines apply a load waveform to a product and measure the corresponding response. The precise and reliable waveform input provided by Shimadzu dynamic testing machines and controllers allows identification of even slight differences in product performance and helps provide feedback for product design.
For example …
A variety of parts is used to achieve a comfortable ride in automobiles. To improve the performance of those parts, data from evaluating their characteristics is essential. Therefore, the damping force is measured as test frequency is varied. Shock absorber performance can be confirmed by measuring the relationship between velocity and damping force or the response to a Lissajous or other waveform. The input waveform is important for evaluating slight differences in performance.
Impressive Waveform Reproducibility
The 10 kHz high-speed feedback and 24-bit high resolution provides highly precise control waveforms for all measurement ranges.
Tests can be done with accurately controlled waveforms even in cases where the frequency of the input waveform varies, such for assemblies or finished products, or If tests are affected by servo valve frequency characteristics or PID control settings are inadequate, then the amplitude can vary depending on the frequency, as shown above. However, the frequency-sweep AGC function corrects the amplitude to keep it constant at all frequency levels.
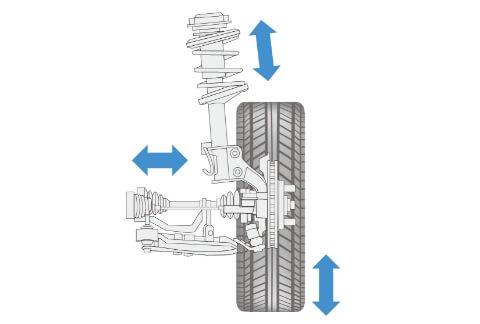
Input waveform

EHF-U Series
Electric-Hydraulic Dynamic and Fatigue Testing System
EHF-U Series
Two-Axis Shock Absorber Testing System
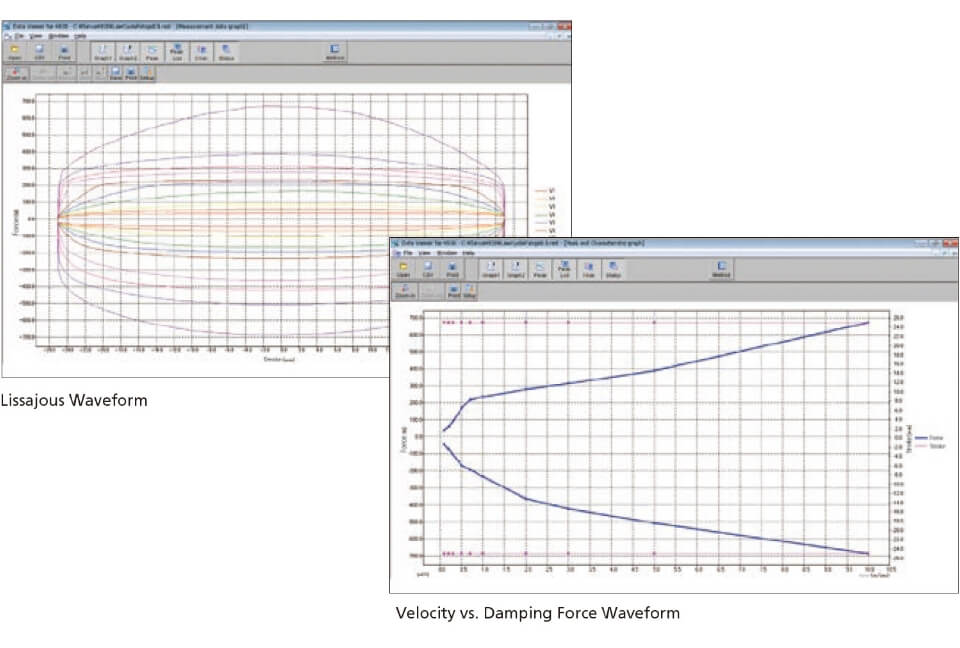
Waveform
Lissajous Waveform
Velocity vs. Damping Force Waveform
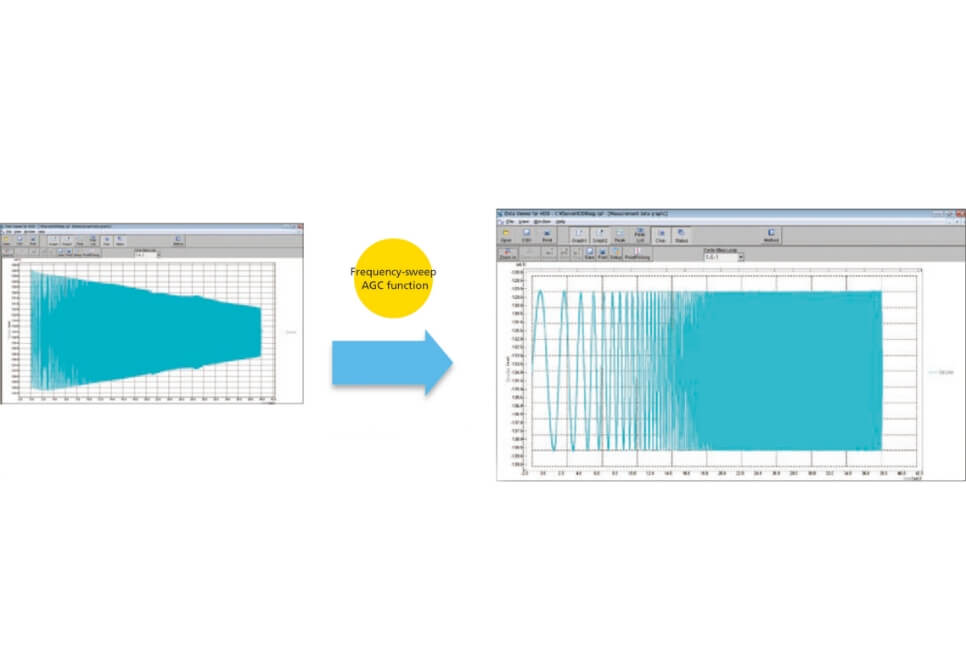
Impressive Waveform Reproducibility
Dedicated Shock Absorber Testing Software
Evaluate Product Endurance in Any Manner Desired
Endurance testing requires a wide variety of testing inputs in order to evaluate the reliability of products or assemblies or to verify design specifications. Shimadzu’s light-weight and compact hydraulic actuators can be installed on a wide variety of stands and used to generate test inputs that closely approximate the conditions under which samples are used. Therefore, they satisfy a wide variety of testing requirements, such as for actuator installation, loading mechanism design, multi-axis synchronized actuator testing, and multi-sample batch testing.
Two-Degree-of-Freedom PID Control Minimizes Effects from External Disturbances
The control method (two-degree-of-freedom PID control) is able to optimize the target response for specified signals and the response to external noise. Optimizing the control parameters using the autotuning feature helps maximize the system performance. The 24-bit high-resolution measurement function and 10 kHz high-speed feedback ensure that even sharp changes in test force or stroke can be controlled reliably.
Autotuning Function
The riding comfort of automobiles is directly related to reducing the amount of vibration and noise. Synchronizing multiple actuators using the Servo Controller 4830 allows accurately simulating the dynamic waveform experienced by parts and components during actual travel.
This allows users to perform 3-axis endurance tests with forces in axial and torsional directions to evaluate the endurance of rubber bushings, which are exposed to forces in various directions. The interference correction function permits tests using waveforms that are even closer to target waveforms.
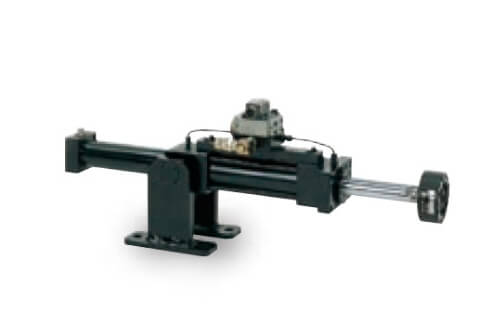
With a trunnion bracket
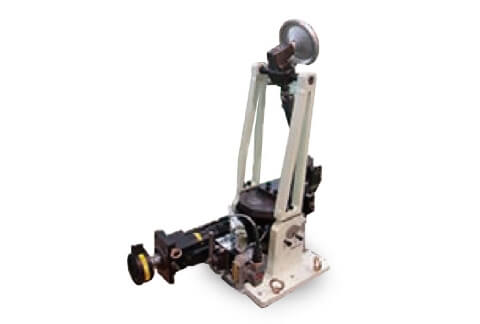
With vertical movement and left/right rotation mechanisms
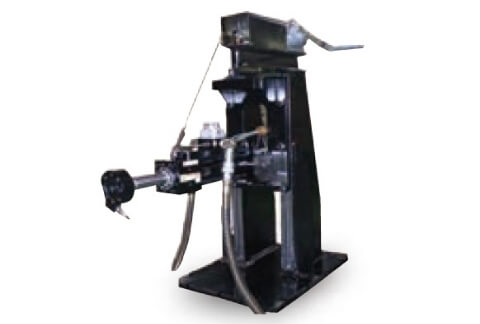
With vertical and left/right rotation mechanisms
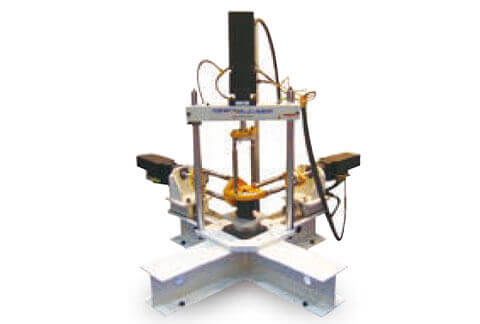
XYZ 3-axis loading frame
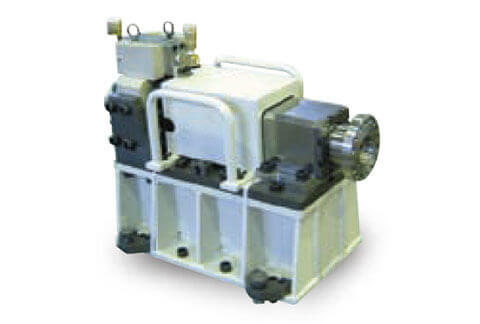
Portable torsional actuator
Accurately Reproduces Actual Operating Waveforms
The Servo Controller 4830 has a waveform correction function that helps accurately reproduce input waveforms. Used in combination with various additional software, it can be used to simulate actual operating waveforms determined by measuring the status of actual loads or simulate the most severe conditions by continuously applying loads at the resonant frequency. The Servo Controller 4830 optimizes actuator control based on various testing requirements to enable highly precise and accurate testing.
Waveform Distortion Correction
This function makes it possible to correct the waveform based on the frequency characteristics of the loading mechanism (transfer function correction), which helps achieve the intended target waveform. Because it can correct for loading mechanism-specific periodic strain, it can cancel out unwanted strain components and accurately control loads according to the target waveform. Complicated actual loading profiles that were difficult to simulate can now be specified easily using this controller and software.
Guaranteeing Endurance
Simulates the Most Severe Loading Conditions Using the Resonance Frequency Tracking Testing
To guarantee product endurance, the resonance frequency is input because it results in the highest load levels. The resonance frequency can be determined in only a few seconds. It can also be automatically tracked if it changes due to sample fatigue. This reduces the labor required to manually specify the resonance frequency and the stress on samples.

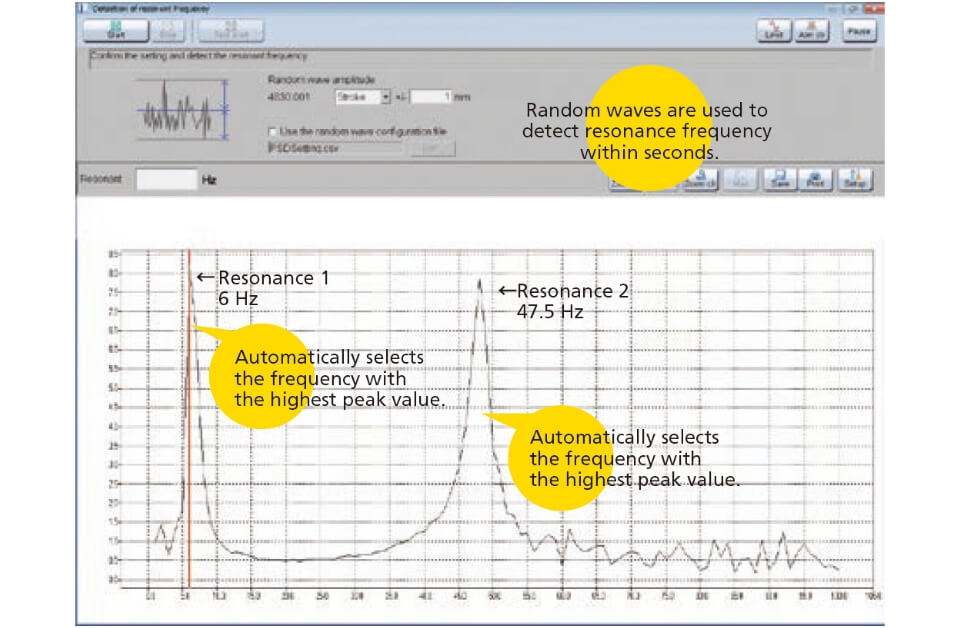
Extensive Experience in a Wide Variety of Fields
From dynamic testing in automotive, aircraft, train, shipbuilding, healthcare, and construction fields to fatigue testing of materials, Shimadzu has developed various dynamic testing machines for all sorts of fields. Shimadzu’s extensive dynamic testing experience is available for consulting with customers.
Dynamic Evaluation of Automotive, Aircraft, Rail, Ship, and Various Other Transportation Equipment
Increasing the reliability of transportation equipment used to carry people and freight involves a variety of dynamic testing requirements, from various design verification work to evaluation of endurance. Shimadzu dynamic testing systems can be configured to meet unique customer requirements by combining various standard models or utilizing customized actuators and loading frames based on Shimadzu’s extensive track record and experience.
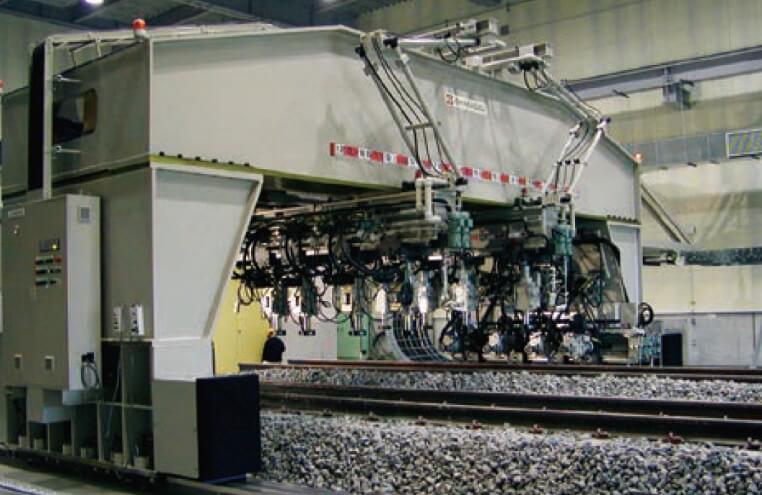
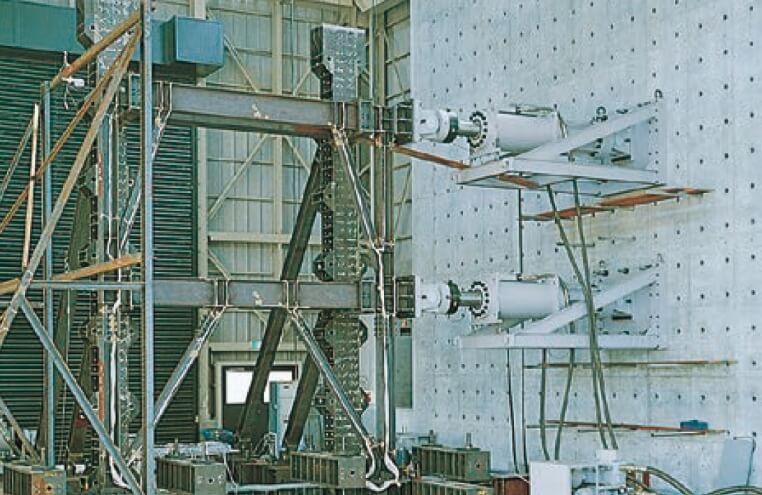
Load Testing for Large-Scale Structural Members
The ground strength, bearing capacity of pilings, stability of basic structural members, etc. are evaluated by applying static and dynamic loads on large structural members using the Shimadzu Servopulser jack system to determine the relationship between test force and displacement. For load testing, actuator endurance and stable control technology are essential. Shimadzu offers support for a wide range of evaluations, such as evaluating structural members made with new materials, evaluating the endurance of large-scale structural members, and inspecting old building structural members.
Evaluating Implants and Biological Materials
Implants and other products in the biomedical industry must be subjected to various design verification testing and endurance evaluation before they can be released to the market. Shimadzu electromagnetic force and pneumatic Servopulser systems are ideal for clean environments and are capable of highly accurate testing at low load levels. Therefore, they are used to evaluate the endurance of knee, hip, and spinal implants or in human kinematic research.
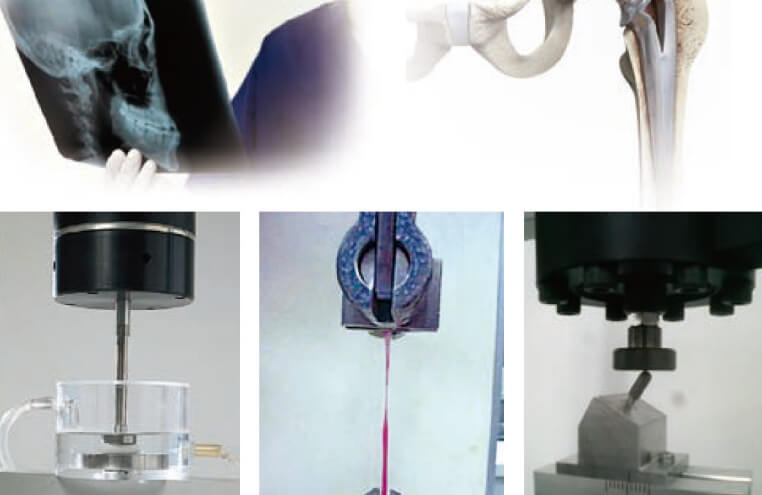
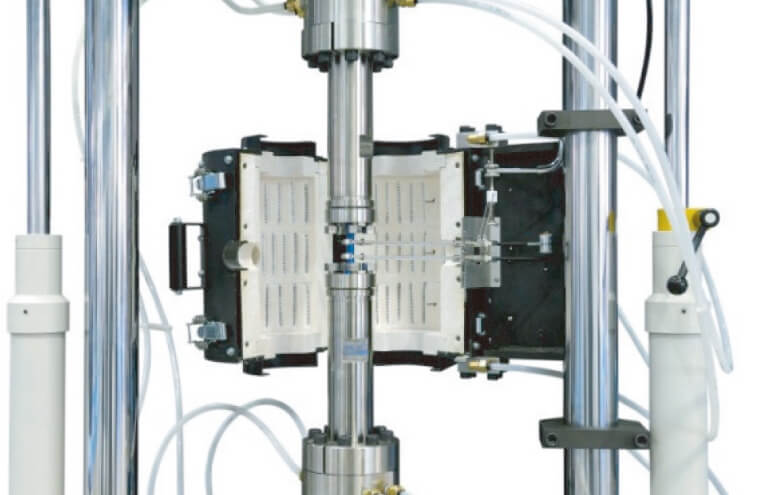
Dynamic and Fatigue Testing in Controlled Atmospheres
Servopulser systems can be fitted with an environmental control system that reproduces loads under high temperature or severe environmental conditions or under environmental conditions experienced during actual usage. This system accommodates a variety of testing requirements, such as testing at high temperatures, in a vacuum or gas atmosphere, or thermal fatigue testing.
Extensive Experience in a Wide Variety of Fields
In order to accommodate increasingly sophisticated designs, computers are now being used in design simulation technologies. In particular, to ensure safety with respect to impacts or determine the behavior during impact fracture, material property parameters are measured at speeds experienced during actual operation or the simulated deformation rate. Using these parameters in calculations can contribute significantly to calculation results.
High-Speed Impact Testing at Speeds Up to 20 m/sec
This high-speed impact testing system integrates several of Shimadzu’s advanced technologies, such as actuators engineered for high-speed testing and shock-absorbing mechanisms that minimize the effects from impact testing, to realize a maximum impact speed of 20 m/sec (72 km/h).
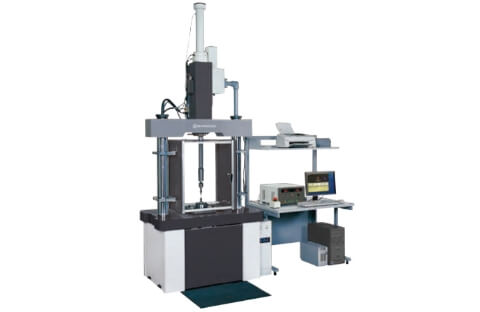
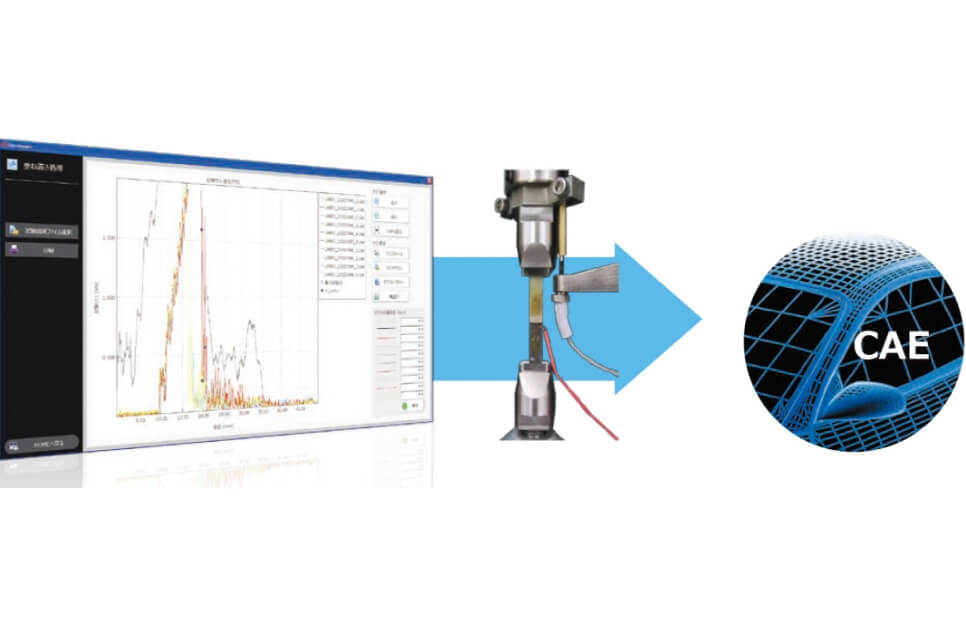
For Reducing the Time Required for Fatigue Testing of Metal Materials and Gigacycle Fatigue Testing
Now that materials used in products are procured from around the world, it is especially important to evaluate the material properties when receiving materials. With cycle rates up to 20 kHz, the USF-2000 Ultrasonic Fatigue Testing System is able to accelerate fatigue life evaluations of metal materials. This means it can perform tests of 1010 cycles, which would normally take 3.2 years at 100 Hz, in only six days. This exceeds the gigacycle level to achieve ultrahigh efficiency.
For example …
Assume a 108 cycle test is performed at 20 Hz and 20 kHz.

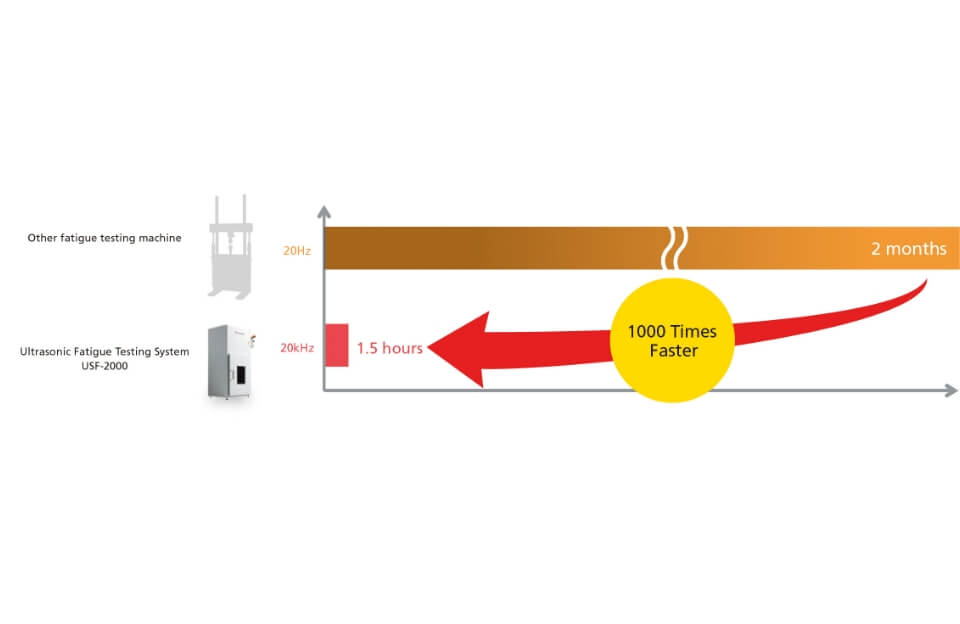
Electric-Hydraulic Dynamic and Fatigue Testing System
Servopulser series electric-hydraulic dynamic and fatigue testing systems feature servo-hydraulic actuators, which are able to accurately reproduce input waveforms. Therefore, they are highly accurate in applying loads ranging from low to high. From high-performance standard models to products customized to satisfy various unique testing requirements, these systems support a wide range of dynamic testing applications.
High Capacity and Compact
By controlling the ow rate of oil, compact hydraulic actuators can apply large forces at a wide range of testing speeds, from extremely slow to very fast. This means they can be used for a wide variety of testing applications.
High-Rigidity Frame
A very rigid loading frame is used to prevent buckling samples. This ensures high reliability for a variety of testing applications.
From Low to High Speeds / From Low to High Loads
High-performance servo valves allow seamless and immediate change of the test force or speed.
An Energy-Saving Operating Mode Is Also Available
By using the optional energy-conservation unit (ECU) (page 36), an energy-saving mode can be used to optimize the hydraulic power supply unit’s power level based on the testing parameters and testing status. It reduces the hydraulic power supply unit’s power level when tests are in standby mode.
Basic Con guration of Servopulser Series Electric-Hydraulic Systems
By selecting (1) a loading frame, (2) a hydraulic actuator, (3) a controller and software, and (4) a hydraulic power supply unit, Servopulser series electric-hydraulic systems are able to accommodate a wide variety of test force and testing speed requirements. The hydraulic drive actuator, which is electrically controlled via a servo valve, provides reciprocating motion capable of high test forces and a wide response range, from low to high frequency.
*Items marked with an asterisk are included based on the
actuator and hydraulic power supply unit combination.
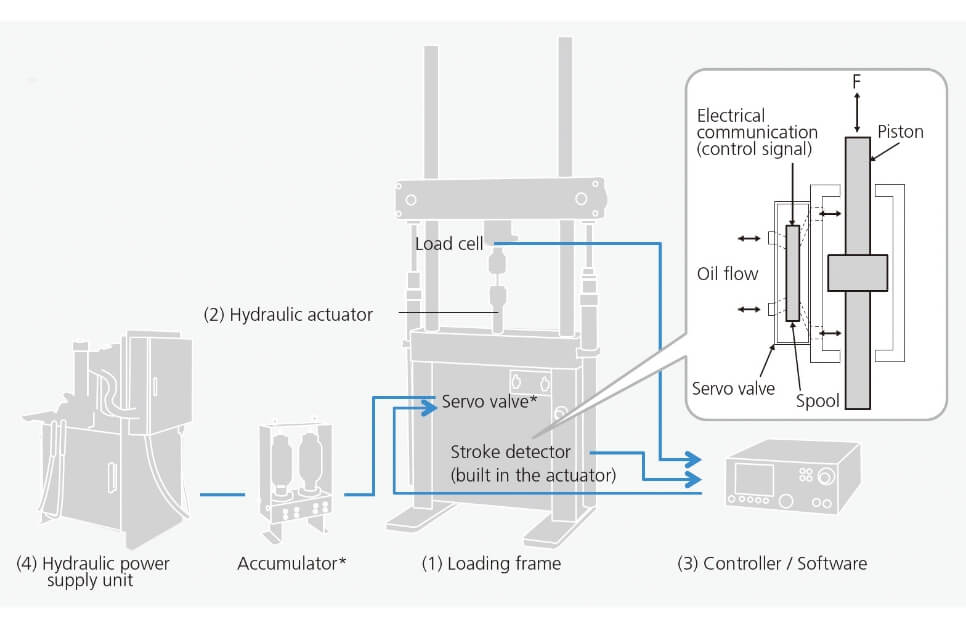
EHF-E Series
For Dynamic and Fatigue Testing of Various Materials and Small Parts
This series features an E-type frame with a bottom-mounted actuator, which can satisfy a wide variety of dynamic and fatigue testing requirements, from fatigue testing of materials to evaluating the performance of components.
Dynamic Capacity Rating of Actuators50 kN / 100 kN / 200 kN
This series is capable of static, dynamic, and fatigue testing of a wide range of materials, from plastics to aluminum, composites, and steel.
1. High Rigidity and Large Testing Space
The large testing space supports material fatigue testing in a high-temperature or thermostatically controlled environment, thermal fatigue testing, fracture toughness evaluation, component performance and endurance testing, and so on. Accessories for respective tests are available. These include grips, compression plates, extensometers, and testing environmental control systems.
2. ±0.5 % Test Force Accuracy
Test force accuracy is guaranteed to within ±0.5 % of the indicated value.
3. Bottom-Mounted Actuator
This supports a wide variety of tests, including component tensile, high/low cycle fatigue, failure, performance, and endurance tests.
4. Dual-Stage Crosshead Drive Mechanism
The hydraulic crosshead drive and hydraulic clamp can be operated more intuitively using handles. This dual-stage con guration helps prevent operating errors and accidents.
5. High-accuracy column
6. Automatically lifting/lowering hydraulic crosshead
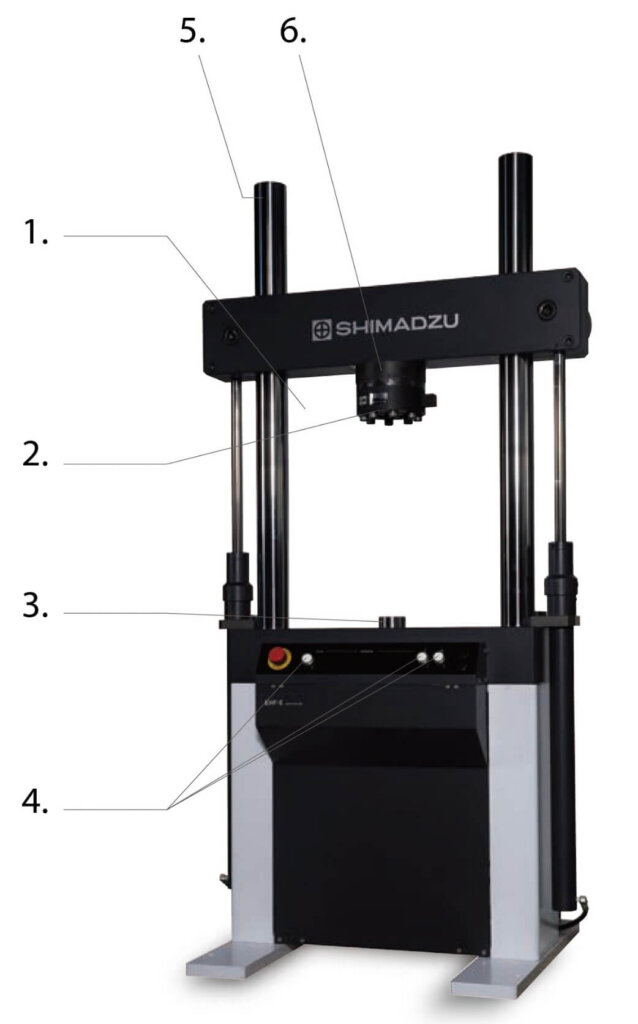

Resistance Heat High-Temperature Testing System

High-Frequency Induction Heat
High-Temperature Testing System
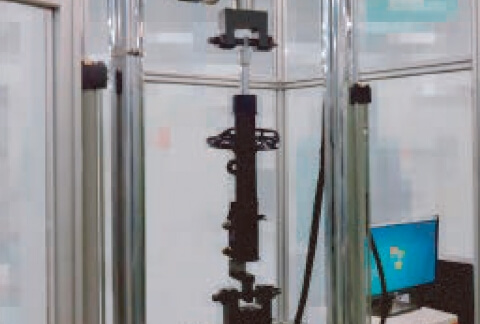
High-Frequency Induction Heat
High-Temperature Testing System
Amplitude Characteristics (60 Hz)
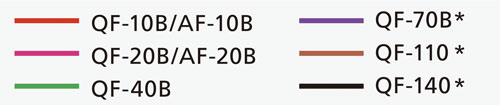
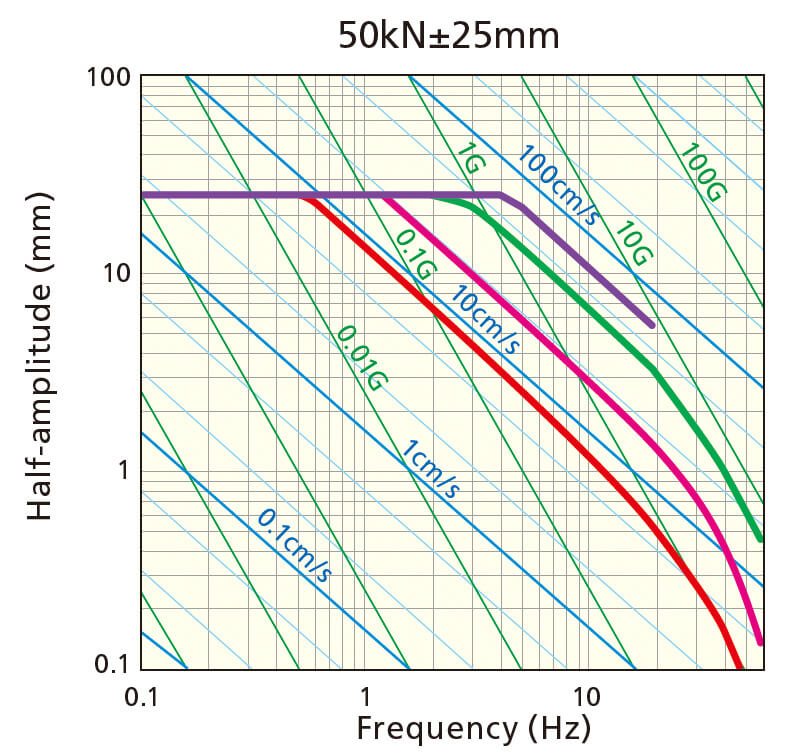
50kN±25mm
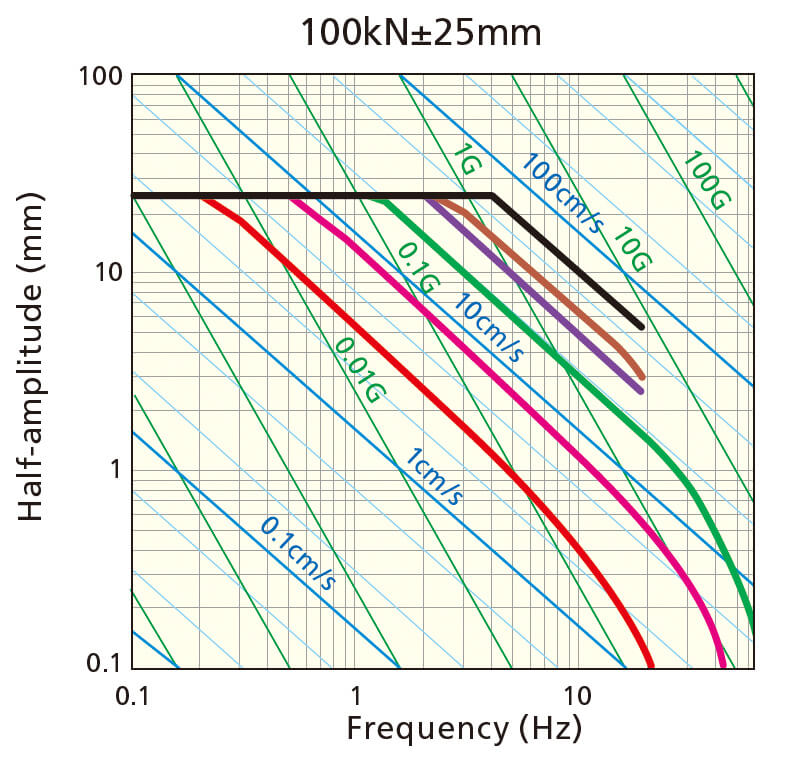
100kN±25mm
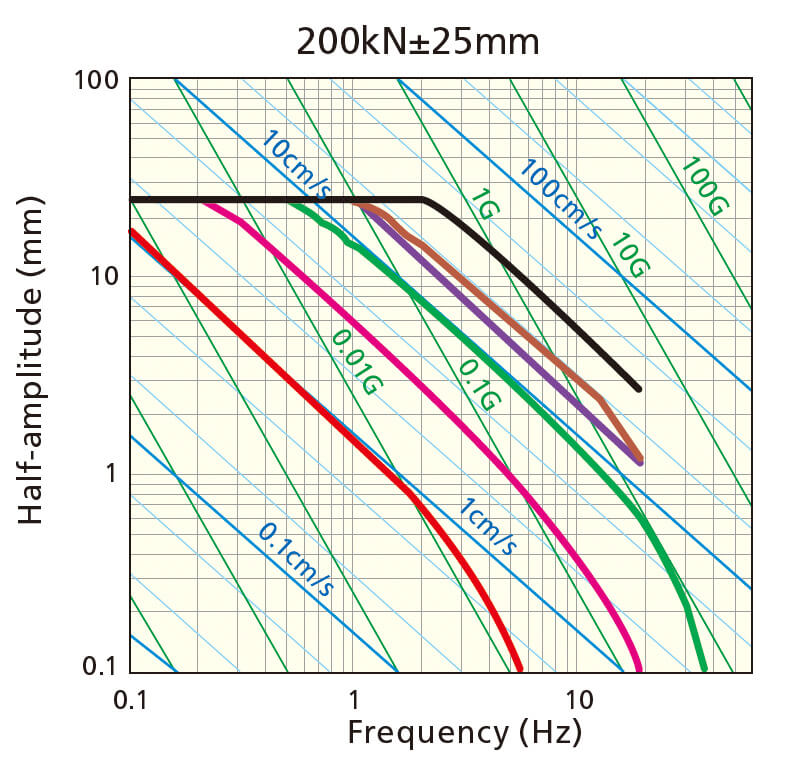
200kN±25mm
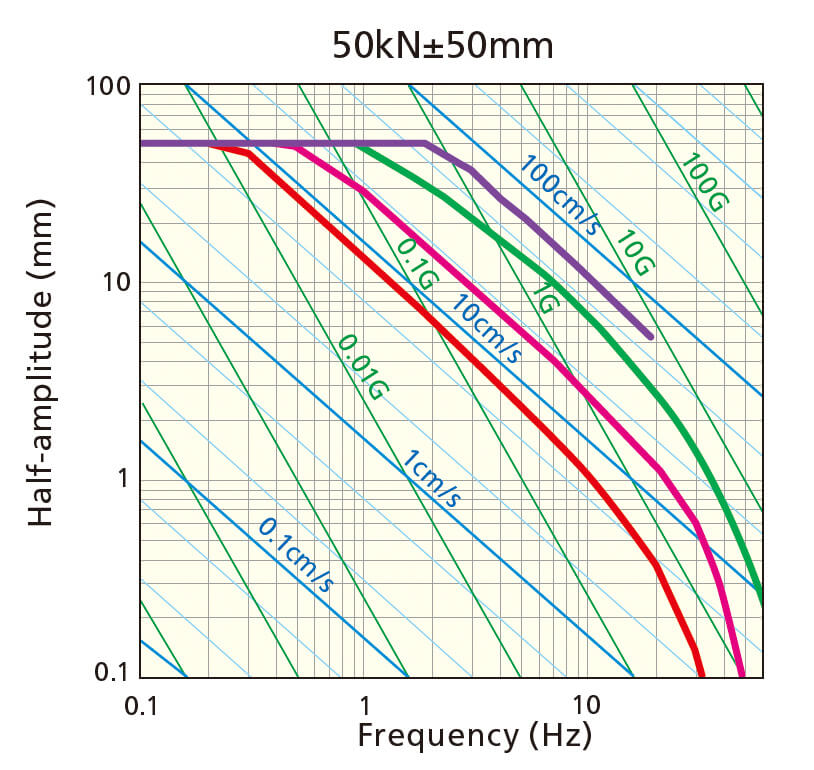
50kN±50mm
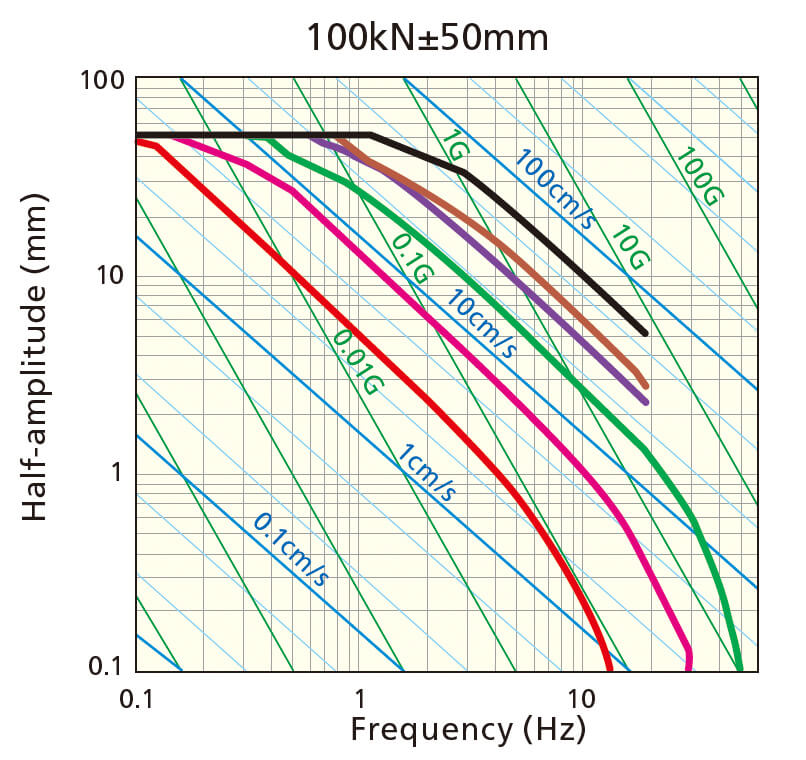
100kN±50mm
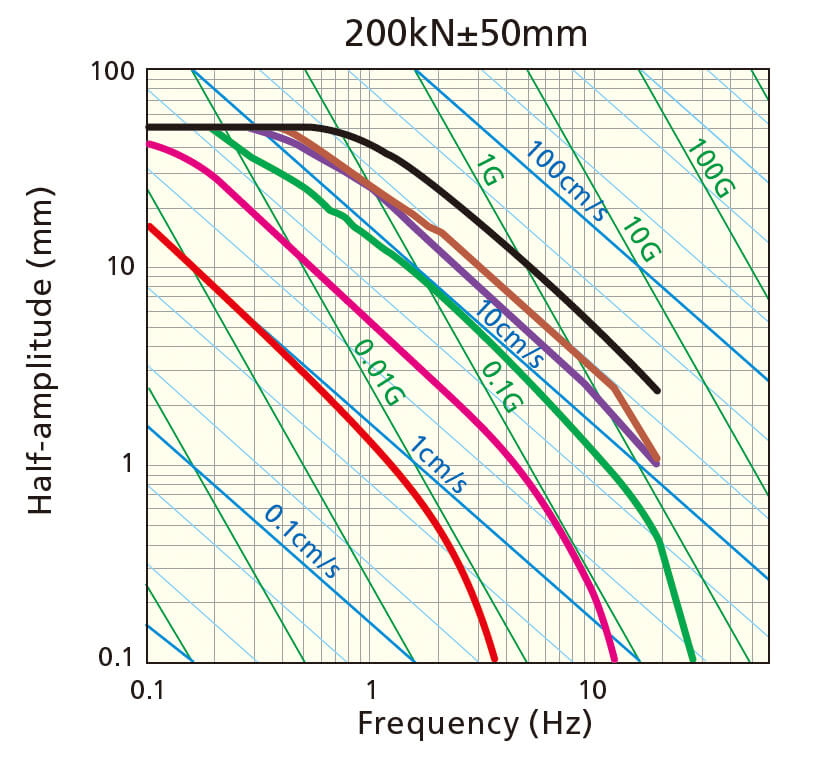
200kN±50mm
* It is not possible to use standard configurations of models QF-70B or higher for high-frequency regions due to the servo valve characteristics. However, these models may be used for testing at high
frequencies if the servo valve is changed, for example. Contact Shimadzu for more information.
- The above characteristic curves indicate the relation between half-amplitude and cycle speed, given sine wave motion at the rated load level.
- The above indicates the amplitude characteristics given a 60 Hz power supply. Characteristics with a 50 Hz power supply will be about 5/6 of indicated values.
- The above characteristics do not include the frame or load cell characteristics. Compensate for the influence of these factors to determine actual amplitude characteristics.
- The indicated characteristics values were calculated based on typical characteristics of the servo valve being used, which may result in a difference of about 10 % on the frequency axis.
- There may be limitations on testing frequencies, depending on jig, sample, or other characteristics.
- At the installation site, provide about 500 mm of space on all four sides of the system, in addition to the space requirements indicated above, to allow access for operation and maintenance.
- The drawing above indicates the dedicated space requirements. The shape and orientation of the hydraulic power supply unit may vary depending on its capacity.
- For a more detailed standard layout drawing, contact Shimadzu.
- The standard system configuration does not include the table, computer, or printer.