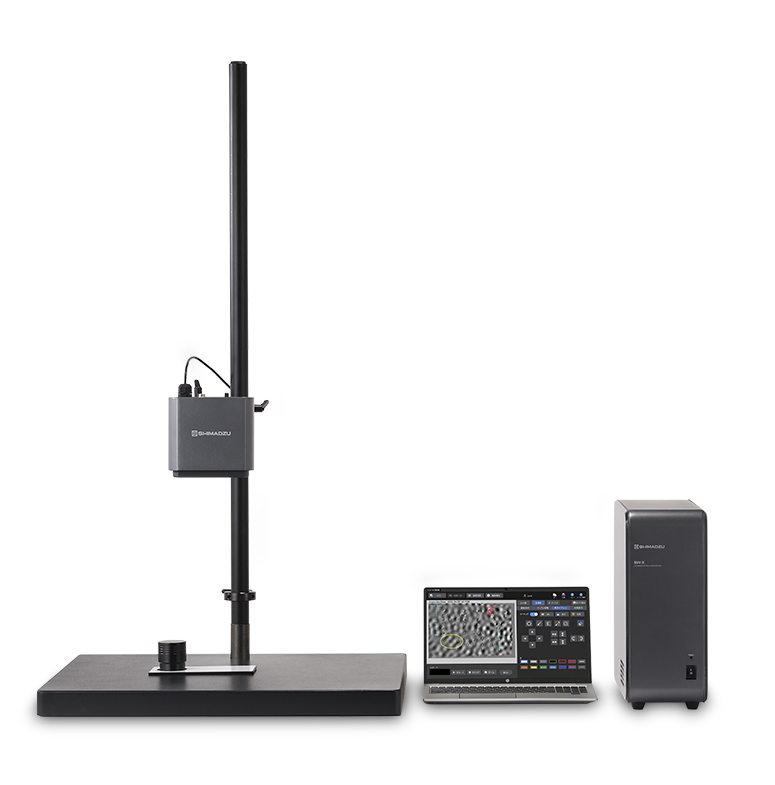
MIV-X
MAIVIS Ultrasonic Optical Flaw Detector
Frequency | 20 kHz – 400 kHz |
Test type | Visual Surface Inspection |
Type | Table-top appliances |
Industries | Transport, Material, Chemicals, Semiconductor, Electrical, Infrastructure |
Enables inspections according to the object size
- Using a Camera Stand for Small Objects
- Attach to Tripod for Large Objects
Make It Visible!
Visualizing Cracks, Voids, Delamination, and Other Hidden Defects Normally Impossible to Check Visually
Utilized in Various Industries
Anyone Can Quickly and Easily Perform a Visual Surface Inspection
Thanks to Shimadzu’s proprietary light imagining technique, which combines an ultrasonic oscillator with a stroboscope, defects near the surface of a material, including peeling of the bonding and adhesive surfaces of heterogeneous materials, as well as paint, thermal sprays, and coatings can be inspected easily and non-destructively.
- Simply attach the ultrasonic oscillator to the sample, and position the camera above the inspection surface.
- The propagation of the ultrasound is quickly displayed, and flaws are easily identified from the video.
- The easy-to-operate software is enhanced with functions to mark the flaws and measure the size easily.
- The lineup includes an optional optical zoom set, which can detect smaller flaws.
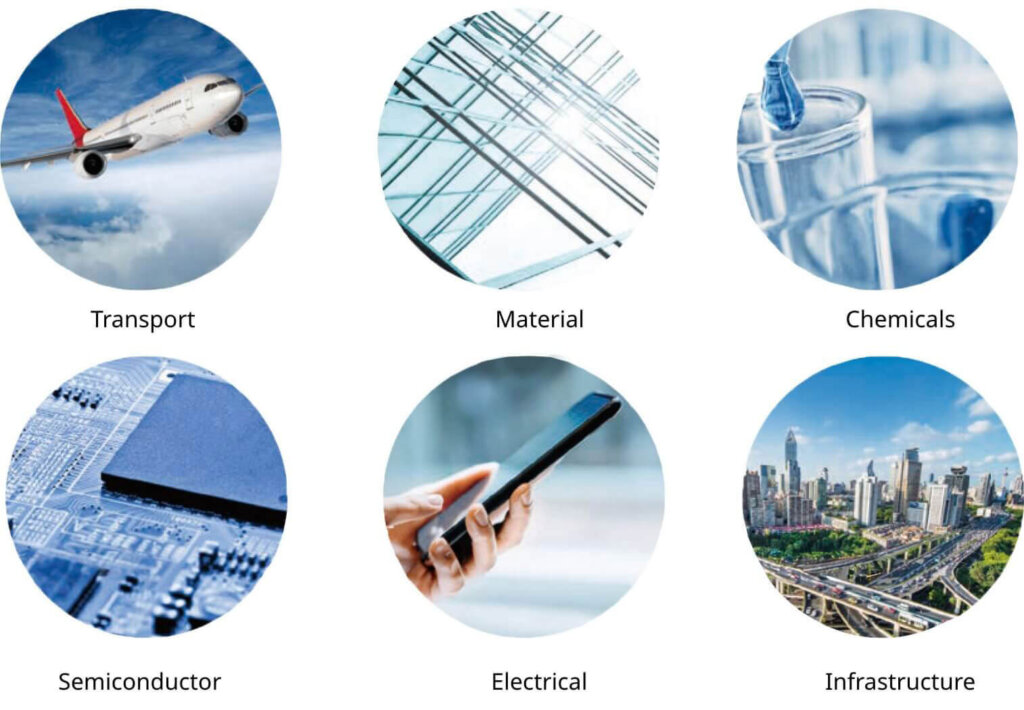
Ultrasonic Optical Flaw Detector MAIVIS™
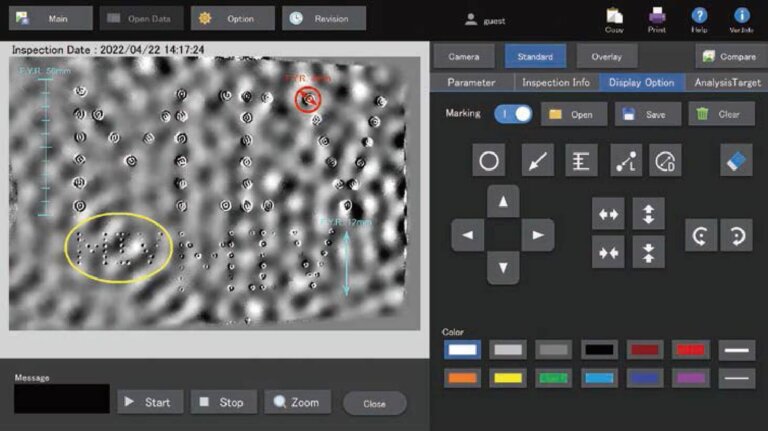
Inspection Case
01 Inspection of Poor Jointing of Dissimilar Materials
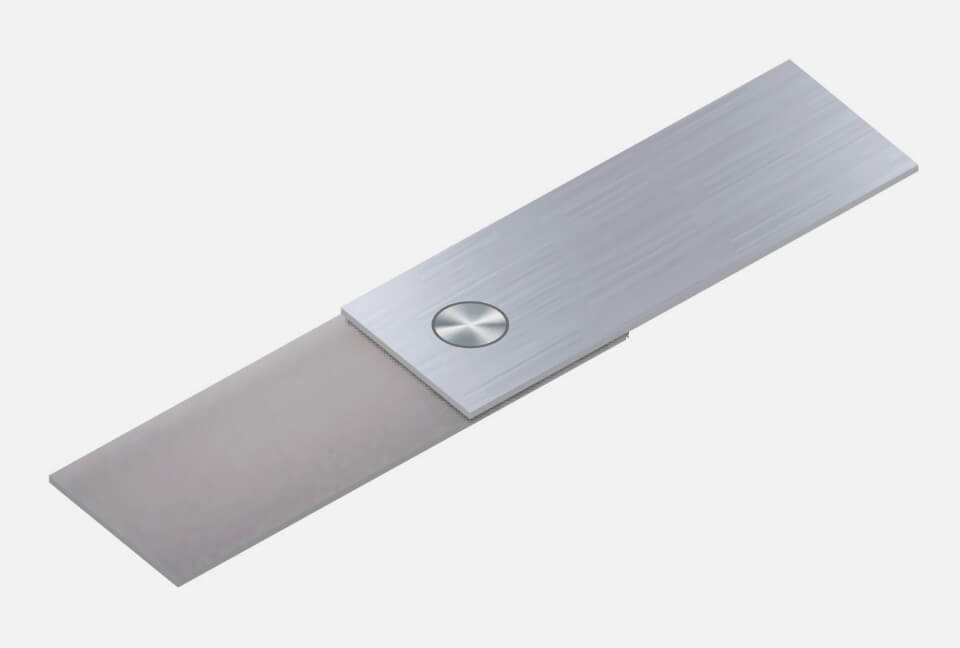
Inspection results
(ultrasonic field image)
Friction stir spot weld (FSSW)
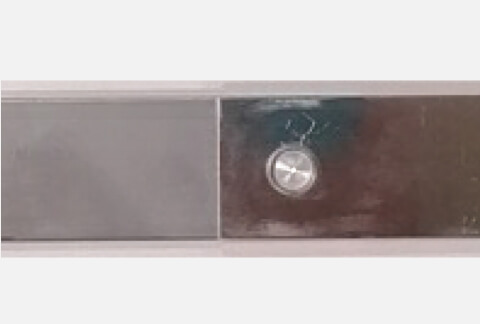
Inspected sample surface
- Aluminum
- Steel
- 30 mm
- Plate thicknesses of 1 mm each

Inspection results
(ultrasonic field image)
Blue frame: Defect region
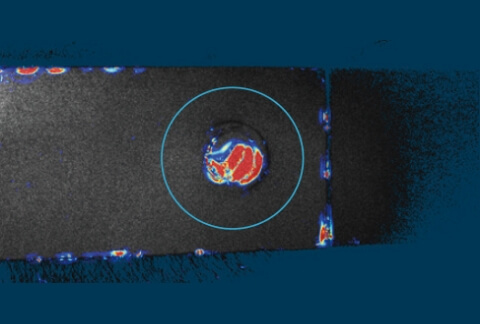
Overlay
Blue frame: Defect region
02 Inspection of Cracks in a Base Material Below a Film (Simulated Coating)
A crack in the surface of a base material below a film (coating), which was not visible to the naked eye, is detected without peeling back the film.
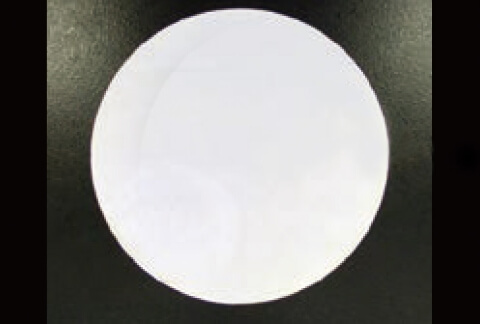
Inspection results
Steel plate with lm af xed
(Simulated crack on the steel plate)

Inspected sample surface
(ultrasonic field image)
Oscillator

Inspection results
(ultrasonic field image)
Blue frame: Flawed region
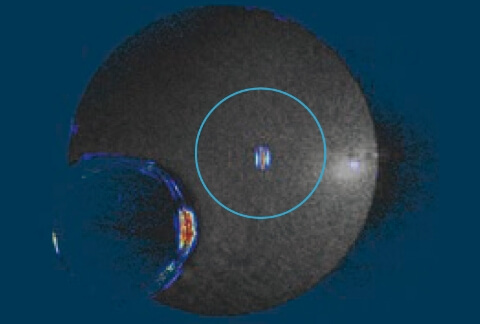
Overlay
Blue frame: Flawed region
03 Inspection of Adhesive Surface Delamination between CFRP and Stainless Steel
Artificially created delamination is detected non-destructively. Further, with X-ray fluoroscopy, unconfirmed delamination (bottom right) is also detected
Sample provided by: Nagoya Municipal Industrial Research Institute
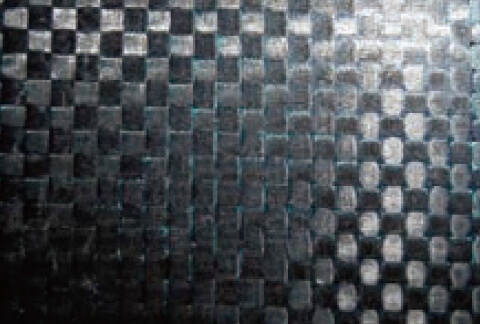
Adhesively bonded CFRP/ stainless steel material (CFRP surface)
Plate thickness / CFRP: 2 mm / Stainless steel: 0.5 mm
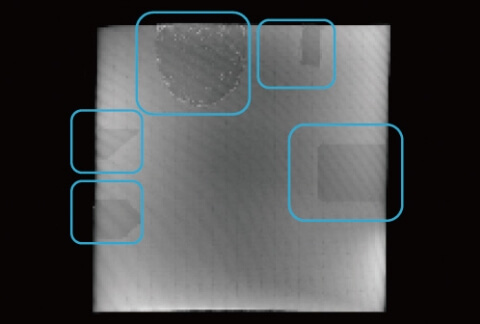
X-ray fluoroscopic image
Blue frame: Simulated defect
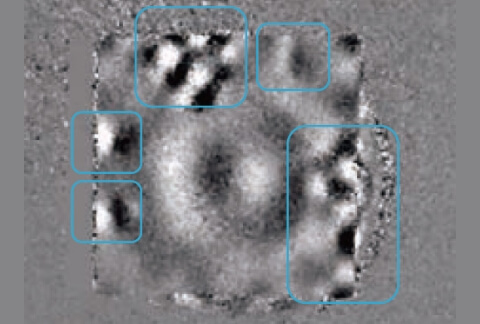
Inspection results
(ultrasonic field image)
Blue frame: Defect region

Overlay
Blue frame: Defect region
04 Inspection of Adhesive Surface Delamination between CFRP and Titanium Alloy
A defect thought to be delamination due to a 3-point bending load is detected non-destructively.
It is evident that the delamination is significant at the center of the loaded region.
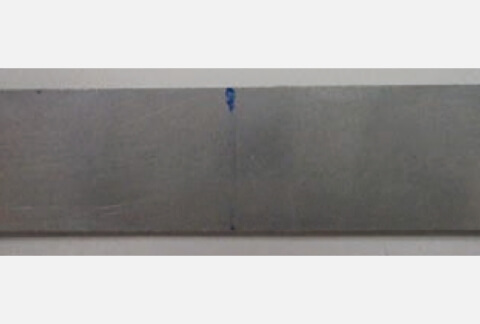
Adhesively bonded CFRP/
titanium alloy (titanium surface)
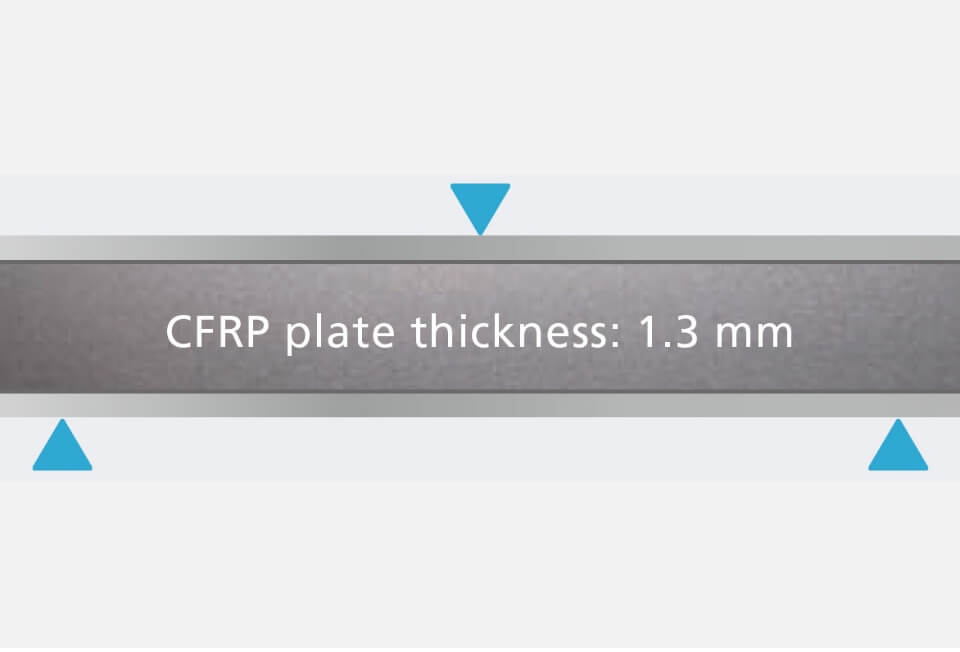
3-Point bending load before inspection
Titanium plate thickness: 0.2 mm
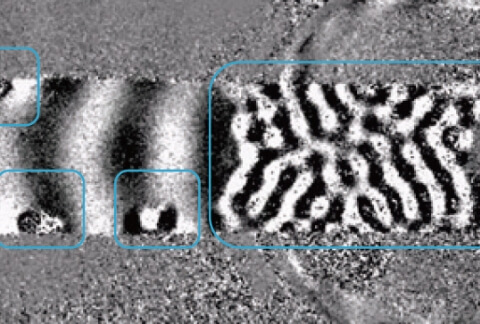
Inspection results
(ultrasonic field image)
Blue frame: Defect region
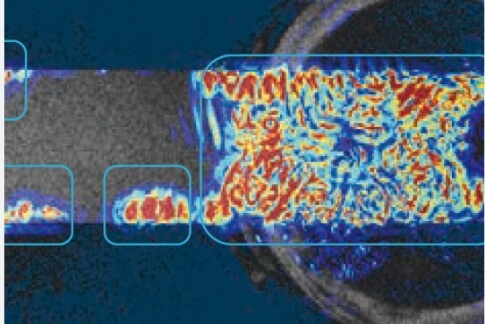
Overlay
Blue frame: Defect region
Measurement Principle
With ultrasonic optical flaw detection technology, the sample is encouraged the displacement of the surface is detected optically, and the propagation of the ultrasonic wave on the surface is observed.
- The sample is loaded by continuous ultrasonic vibrations.
- Microscopic out-of-plane displacement of the surface due to propagation of the ultrasonic wave is visualized optically using laser irradiation and a camera*.
- Defects are detected by observing disturbances in the propagation of the ultrasonic wave.
*Shimadzu’s proprietary light imaging technology combines speckle shearing interferometry via ultrasonic vibration with a stroboscopic technique. (Patented in Japan, China, and the USA)
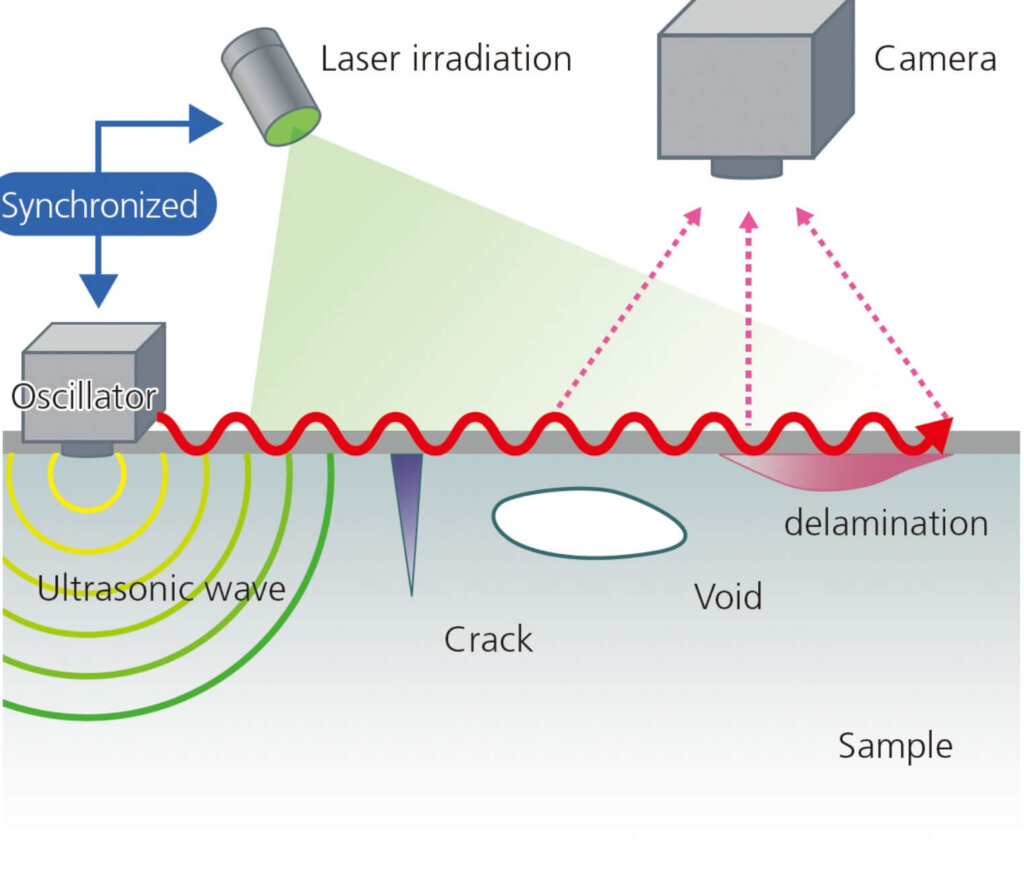
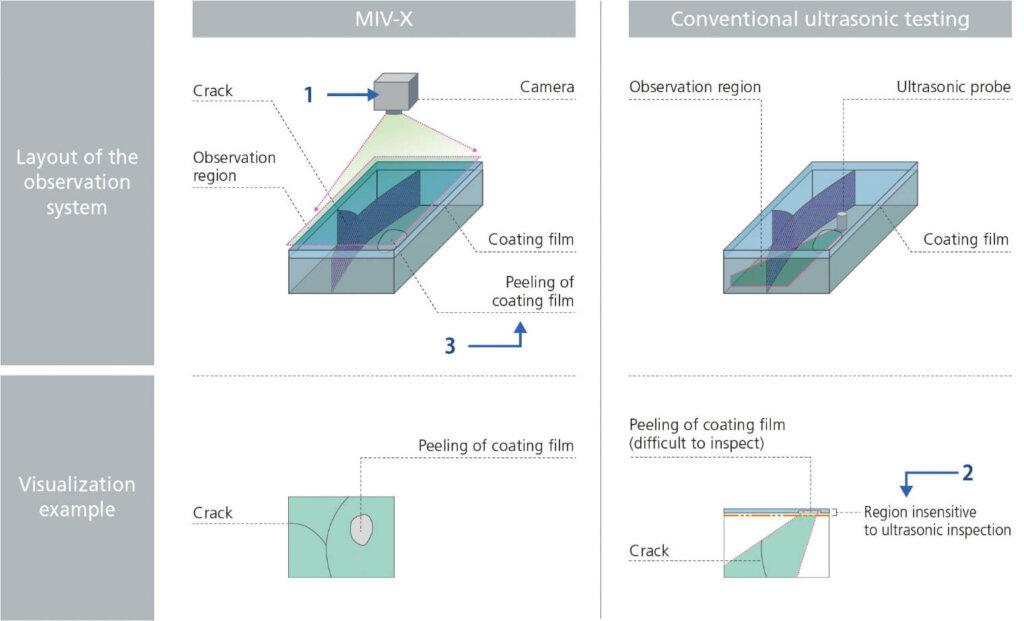
Difference from Ultrasonic Flaw Detection
The MIV-X Ultrasonic Optical Flaw Detector assists with regions where ultrasonic testing (UT) is difficult.
Leave the non-destructive inspection of surfaces and near surfaces to MIV-X!
Here are the advantages!
1 Batch inspection of a wide area within the camera’s field of view
2 Good at inspecting surfaces and near surfaces
3 No need to worry about differences in acoustic impedance even for dissimilar materials
Useful Functions
Noise Removal Function Simplifies Defect Identification
Observation sample:
- Plate with film affixed.
- The plate is engraved with the characters „MIV“ in three places. (with engraved diameters of 1, 2, and 4 mm).
- (The region with the engraved MIV is marked with a red frame.)
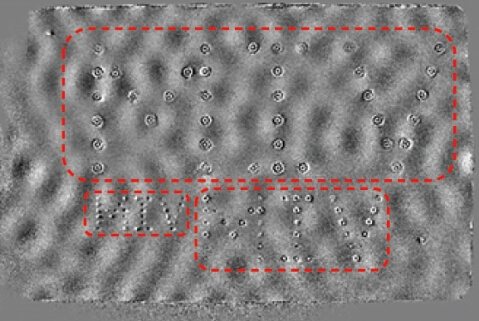
Standard image
(ultrasonic field image)
Some noise remains
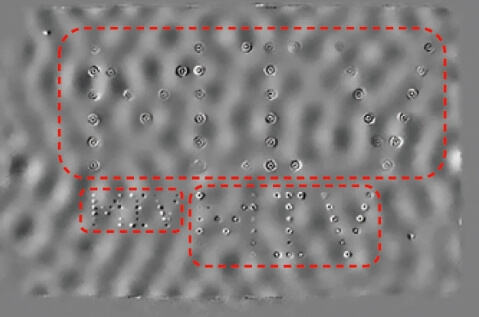
Noise removal ON
The noise is removed, leaving a clear image
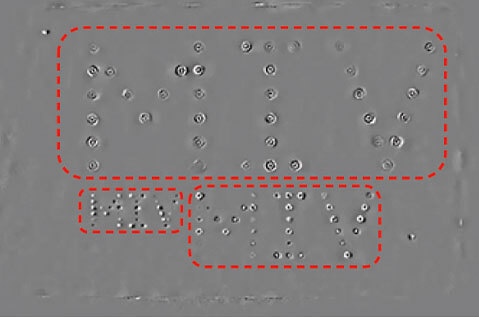
Background wave filter ON
Image with highlighted text
Dimension Display and Marking Functions Simplify Identification of
Defect Position and Size
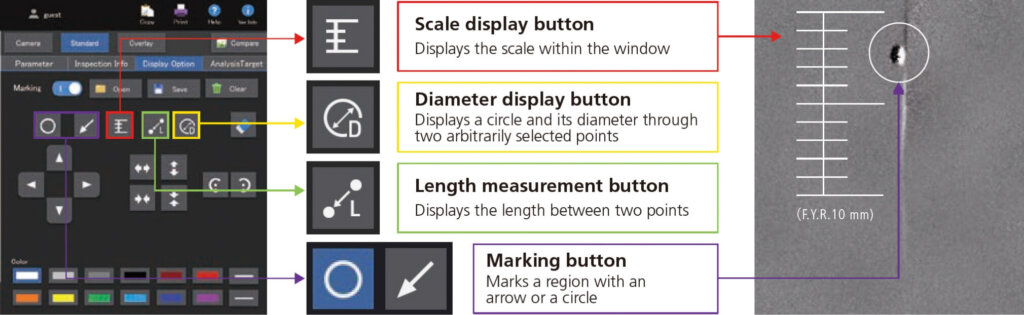
Optical Zoom Set (Optionally Available) for Detecting Smaller Defects
Decreases the minimum detection size by a factor of approximately two (MIV-X standard: From approximately
1 mm dia. to 0.5 mm dia.)
Laser optical axis adjustment is also possible, improving irradiation uniformity
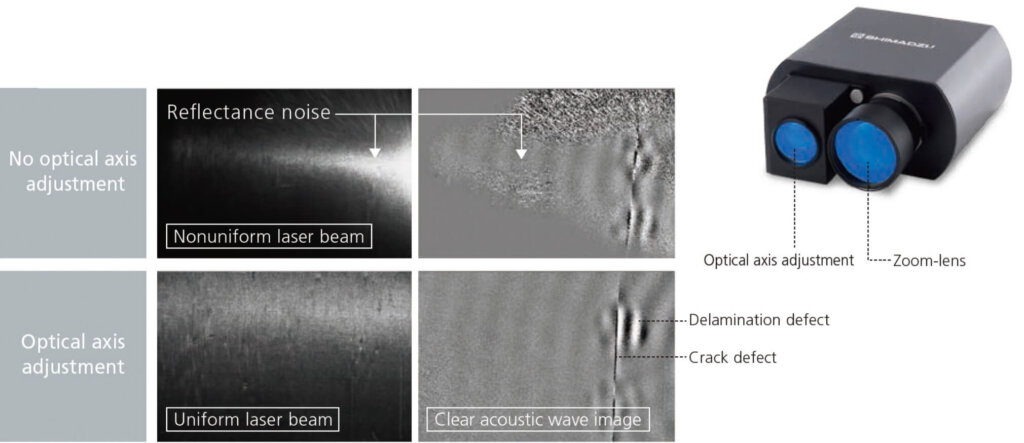
Applications
Options
MIV-X Universal set 331-30400-58 | ||
---|---|---|
Camera stand | 331-30450-42 | Maximum camera distance 1000 mm, With camera angle adjustment mechanism |
Optical zoom set | 331-30410-42 | Camera distance: 50 to 200 mm, Inspection area: Approx. 28 × 42 mm (camera distance 50 mm), Minimum detect size: φ0.5 mm (depends on sample and inspection condition) |
Technical data: MIV-X
![]() |
|||
MIV-X | |||
---|---|---|---|
Use | Detection of defects such as voids and cracks near the surface of a sample and peeling of joining area of multimaterial | ||
Inspectable material | Metal, Ceramics, Composite, Dissimilar joint, Multi-material, etc. | ||
Camera distance | 250 to 1000 mm | ||
Inspection area / Curvature radius | Approx.100×150 mm / R150 mm(Camera distance 250 mm) Approx.200×300 mm / R300 mm (Camera distance 500 mm) Approx.400×600 mm / R600 mm (Camera distance 1000 mm) | ||
Minimum detection size | Approx. 1/100 of inspection area (depends on sample and inspection condition) Camera distance 250 mm → Minimum detect size is approx. φ1 mm. | ||
Inspection time | Approx. 25 seconds or less (Observation + Analysis, except condition setting time) | ||
Frequency | 20 kHz to 400 kHz | ||
Laser safety (Class) | IEC60825-1 Class 1, FDA 21 CFR Part 1040.10 Class 1, JIS C6802 Class 1 | ||
Standard function | Frequency scan, Analysis area speciication, Marking, Dimension display, Defect rate calculation, Multi- condition compound analysis, Noise remove, Background wave ilter, Inspection condition automatic search, Data storage / output | ||
Power requirements | Single phase 100 to 230 V, 250 VA Power connection port on the Control unit : IEC60320-C13 | ||
Operating temperature | +10 to +30 ℃ | ||
Dimensions / Weight | Camera unit: 180 mm (W) × 170 mm (D) × 88 mm (H); approximately 2.7 kg Control unit: 165 mm (W) × 390 mm (D) × 406 mm (H); approximately 12 kg Oscillator: 60 mm (Dia.) × 60 mm (H); approximately 0.9 kg |
Technical data: Configuration MIV-X
MIV-X Universal set 331-30400-58 | ||
---|---|---|
Camera unit | 331-30340-11 | |
Control unit | 331-30275-11 | |
Oscillator unit | 331-30178-11 | |
Software | 331-30502 |